联系我们Contact
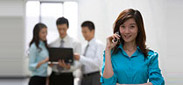
公司名称:东莞市运通环保科技有限公司
加盟热线:+86-769-81550838 \ 85533363
咨询热线:13326859308
邮 箱:deng@dgyuntong.com
网 址:www.dgyuntong.com
地 址:广东省东莞市长安镇乌沙李屋第六经济开发区兴发南路西四街一号
2018/10/23 11:50:35
如何处理大量堆积如山的废旧轮胎,把“黑色污染”称谓的帽子摘掉,变为黑色资源甚至是黑色金矿,是我国面临的一个重要环境与资源利用的课题。
目前我国每年产生废旧轮胎约3亿条,重量达1000万吨,这么大体量的废旧轮胎除回收作旧轮胎翻新循环使用之外,还可生产再生橡胶、橡胶粉、热裂解等利用方式。但废旧轮胎作为汽车工业迅猛发展带来的污染,产生量还将会大幅度上升。
作为过程工业重要的支撑技术之一,粉碎加工设备主要用于解决工业生产过程中诸多以物理变化为主的单元操作装置。废轮胎的三种利用方式,尤其是制作橡胶粉、生产再生橡胶的发展水平,在很大程度上取决于粉碎设备的工艺改进与创新发展程度,也是废轮胎减量化的有效手段。
不过,国内众多设备企业,发展水平参差不齐,真正能做到大型化、系列化、成套化和标准化方向发展的并不多,很难说哪一家能够代表我国粉碎设备的最高发展水平,而制约我国轮胎粉碎设备行业发展的瓶颈问题也显得日益突出。比如,自主研发不够,抄袭山寨仿制泛滥;自动化、智能化程度比欧美发达国家还有很大一段差距等。
一、我国废旧轮胎粉碎设备现状
据市场调查,我国每年产生的废旧轮胎中,生产再生胶与胶粉占了50%左右,而其中再生橡胶的产量又占了近90%的比例。
由于废旧轮胎处理后的应用主要集中在再生橡胶与橡胶粉的生产,而其中再生橡胶所需橡胶粉细度大约在24-30目,而橡胶粉也有很大一部分用在了橡胶粉改性沥青和田径跑道方面,而橡胶粉改性沥青的胶粉细度也在30目左右,田径跑道的胶粒在1-4mm橡胶颗粒,因此我们现在讨论的重点放在生产这些规格的橡胶粉和胶粒的设备配置以及工艺流程方面。
(一)24-30目的胶粉生产设备配置及工艺:
1、目前国内胶粉的很多生产企业还在沿用的“小三件”设备(实际上现在已经是“小两件”了)(切条机+切块机)+沟光辊破胶机。虽然国家现在下大决心进行淘汰“小三件”的宣传工作,取而代之使用安全高效的“双轴破碎机”,但是不可否认的是,现在很多胶粉企业仍然在使用“小三件”。显然,这不仅仅是靠宣传引导就能杜绝“小三件”的使用的,很多胶粉企业向设备制造厂家诉苦,他们不是不想使用“双轴破碎机”,而是一直存在侥幸心里,在没有出现安全事故的时候,使用“小三件”生产橡胶块的成本较低,分析如下:
(1)使用“小三件”的能耗:
“小三件”,按照以前的称呼,是指轮胎口圈切圈机、轮胎切条机、胶条切块机,但是现在的操作工更加简化,已经取消轮胎口圈切圈机,直接把轮胎放在轮胎切条机上面,先把一边的轮胎胎肩切下来,然后把轮胎切成条并打成块,实际上是“小两件”,出料均匀(一般40X50mm),比我们双轴破碎机出料还均匀,每一台切条机装机功率5.5千瓦,切块机7.5千瓦,1分半钟可以处理1个60公斤(已经包括了上、下料等辅助时间)的轮胎,每小时可以处理约2-2.5吨,也就是说能耗为6度/吨轮胎,操作工为1人,购买这两台设备的总价约为1.5万,刀具耗材费用约为10元/吨轮胎。
(2)使用“双轴破碎机”的能耗:
1)双面口圈切圈机7.7千瓦,产量最多2吨;2)双轴机+筛选+进料+回料,总功率99千瓦,产量3吨。能耗为30度/吨轮胎,操作工为1人,购买设备总价约为70万,刀具耗材费用约为30元/吨轮胎。
从上述两种工艺的对比来说,由于胶粉企业的利润本来就很低,而“小三件”在能耗、设备购买价、刀具耗材费用方面都优于“双轴破碎机”,并且由于生产再生胶的工艺特性,全钢丝子午线轮胎胎面胶比胎侧和胎肩胶的质量更好,能生产出更好的再生胶,而“双轴破碎机”只能整体处理轮胎,所以国内很多胶粉生产企业存在着侥幸心里,冒险地使用着“小三件”,对“双轴破碎机”的生产商来说,在国内的推广步履艰难。
现在摆在广大“双轴破碎机”设备生产商面前的是,怎样设计生产出低能耗、低耗材、安全性更高、使用更方便的轮胎处理设备,并能自动把胎面胶分开,让胶粉生产企业真心愿意使用“双轴破碎机”,而不是仅仅依靠呼吁禁用“小三件”。
需要解决几个问题:
对于双轴破碎机的刀具第一次修磨的时间,目前有2种判定方法:1)在耗电相同的情况下,出胶块产量减低很多;2)出现胶块不是被剪断而是被刀扯断的现象。据客户使用经验及测试显示,即使出料胶块出现100%被刀扯断现象,在相同产量的情况下耗电也没有很大的区别,这就引出一个问题——到底刀具使用多少时间才更适合对刀具进行第一次修磨?
来看国外一组数据:1)德国生产制造废旧轮胎处理设备比较先进的KAHL公司,它的客户介绍,每小时处理3.5吨轮胎的双轴机大约处理2000吨轮胎(带止口圈钢丝一起处理)需要进行第一次修复,按照小时换算大约580小时需修复;2)丹麦生产制造废旧轮胎处理设备比较先进的ELDAN公司,它的设备在加拿大多伦多Liberty Tire Recycling公司使用,客户说刀具都是在美国SSI公司(美国SSI公司是美国一个比较专业制造破碎设备的公司)购买,双轴撕碎机的刀盘大约处理6500吨轮胎就需要更换,其中双轴撕碎机产量为20吨/小时,双轴机大约处理6500吨轮胎(带止口圈钢丝一起处理)需要进行第一次修复,按照小时换算大约325小时需修复。
按照一般经验,如果把轮胎口圈去掉后再进入双轴撕碎机撕碎,刀具第一次修磨时间会延长一倍,也就是说德国KAHL公司大约1100小时进行第一次修磨;而丹麦ELDAN公司和美国SSI公司大约650小时进行第一次修磨。
上述这些国外同行的刀具第一次修磨时间,都是在胶块出现被刀扯断达到约80%的时候,并且出料大小大约为50×70mm—50×120mm,而我国使用沟光辊破胶机的胶粉企业,一般要求胶块大小小于50X80mm,如果尺寸太大钢丝太长,沟光辊破胶机下方的胶粉筛不能尽快地将钢丝筛除,使得钢丝多次经过沟光辊而加快了沟光辊的磨损。所以如果按照国内的要求,尺寸大于50X80mm的胶块将再次回到双轴破碎机破碎,因此刀具进行第一次修磨时间将缩短。
不过,不容置疑的是,国外先进公司的刀具使用寿命比国内长,但因为维修费用(包括人工、购买焊丝价格等其他修复费用)比国内高很多,因此每处理1吨轮胎的耗材也基本上与国内双轴破碎机处理轮胎耗材持平。
基于上述各种数据分析,由于“小三件”在一些数据上的优势,而“双轴破碎机”在短时间内又无法超越,要想让广大胶粉生产企业真心实意地淘汰“小三件”,要做以下几方面的工作:
首当其冲的当然是所有“双轴破碎机”的生产商:1)在刀具使用寿命方面要继续花大力气试验更好材料的焊条、焊丝,使得刀具赶上甚至超过国外同行的使用寿命;2)采用在刀座上镶嵌或者可拆卸的刀体模式,方便客户拆卸修复,减低修复时间和费用;3)“双轴破碎机”是否有可能设计成类似于“小三件”切割轮胎这种方式。
其次,作为协会应向国家工信部、财政部、发改委等部门申请:对于橡胶粉生产企业使用 “双轴破碎机”将给予财政扶持补贴,希望能真正带动低能耗、低耗材、安全性更高、使用更方便的轮胎处理设备在国内大量推广。
(二)5-15目(4-1mm)的胶粒生产设备配置及工艺:
前段时间报道的“毒跑道”风波,让不明真相的人把橡胶颗粒和轮胎颗粒视作“毒跑道”的根源,这是极大误解,对于废旧轮胎和废旧橡胶本身来说,是没有问题的,如果是有毒物质粘连在废旧轮胎和橡胶上面,这就不是轮胎和橡胶本身的问题,而且“毒跑道”最大的问题还是出在胶黏剂上。
对于田径跑道颗粒的生产工艺,有人可能简单地认为是不是使用“双轴破碎机+沟光辊(或双沟辊)破胶机”就可以生产胶粒。
其实不是这样,由于田径跑道一般只有13mm的高度,下层10mm使用废旧轮胎颗粒,上面3mm使用三元乙丙橡胶颗粒(EPDM),田径跑道施工的时候只需把胶黏剂与这些颗粒拌合,铺设到路面上,然后使用摊铺机摊平即可。
由于沟光辊(或双沟辊)破胶机在处理废旧轮胎胶块的过程中,主要是通过双辊的搓切和剪切来完成,因此成品胶粒里面大多是毛刺状的橡胶颗粒,而这种毛刺状的橡胶颗粒如果铺设到路面上的时候,将使用更多地胶黏剂从而增加了客户的生产成本。
而使用“双轴破碎机+钢丝分离机(或叫中碎机)+橡胶破碎机(或叫细碎机)”这种工艺流程,由于在处理废旧轮胎的过程中,一直是纯“剪切”的方式,所以橡胶颗粒菱角分明,使用的胶黏剂也大大减少从而降低了客户的生产成本。
所以目前田径跑道颗粒的生产工艺基本上是“双轴破碎机+钢丝分离机(或叫中碎机)+橡胶破碎机(或叫细碎机)”,由于这种工艺流程耗电更大、耗材费用更高,这也解释了一些人很疑惑为什么田径跑道颗粒(1-4mm)销售价现在大约在1400-1700元/吨,而更细一点的20-30目(0.85-0.6mm)胶粉销售价现在约1000-1200元/吨。
二、我国废旧轮胎粉碎设备的发展方向
1. 双轴破碎机:
从目前所有处理轮胎的粗碎设备类型来说,有大家熟悉的“双轴破碎机”、德国骁马机械公司的“单轴撕碎机”和丹麦ELDAN公司生产的“单轴撕碎机”,后两种单轴撕碎机虽然各有优势(主要是更换刀具较方便),但是从能耗和设备稳定性、噪音方面,双轴破碎机更具优势,在以后很长的一段时间内,双轴破碎机还将在粗碎轮胎这一工序里领先其他设备,只是双轴破碎机必须继续在刀具使用寿命和拆卸更方便方面做出更多改进。
2. 钢丝分离机(或叫中碎机):
如果需要生产出好的橡胶颗粒以及在能耗方面,钢丝分离机比沟光辊(或双沟辊)具有更大的优势,目前由于刀具结构的设计,使得该机出料后轮胎钢丝与橡胶存在包裹现象,因此磁选出来的钢丝需再一次使用另外的设备处理,这无形中加大了生产成本及能耗,因此各设备生产商需更优化刀具的结构设计。
比较来看,德国KAHL的设备运行,设备磁选后的钢丝出料里含有较多橡胶,但是后续配置了振动筛分装置把合格钢丝分离,不合格钢丝回到设备里再处理,丹麦ELDAN公司的也类似。如果能一次性地在刀具结构上能解决的话,可能会更好。
钢丝分离机由于是封闭处理轮胎胶块的,由于有钢丝和尼龙,所以在处理轮胎胶块的时候,一定会产生火星,会有起火的隐患,在设计时必须足够重视。
此外,刀具的使用寿命。由于在高速切削带钢丝的橡胶块,刀具磨损很快,虽然现在各国设备制造商都尽量把动刀和定刀设计成“前、后、左、右、上、下”等可以调换使用,已经大大延长了刀具使用寿命,但是在刀具材料以及维修工艺方面,亟需进一步提升。
3. 橡胶破碎机(或叫细碎机):
据统计,国内轮胎子午化率2015年已经达到80%(换算成“吨”后的数据),但是半钢胎(主要指小车胎和货车胎)仍然占了一定比例,而处理这些半钢胎时,如果出料胶粒大于4mm时,出料胶粒里面会不同程度地包裹着一段尼龙线,而带有尼龙线的胶粒既不好看,如果田径跑道颗粒使用的话又会吸附更多地胶黏剂,从而增加生产成本。因此,在半钢胎的处理方面,如何有效地去除胶粒里面包裹的尼龙,需要各设备生产商进行技术升级改进!
4. 沟光辊破胶机:
由于生产30目以内胶粉的主要设备还是沟光辊破胶机,从以前的冷硬铸铁辊到现在既有冷硬铸铁辊,又有铸钢辊在市场上并存。发展方向还是使用铸钢辊,关于焊接材料的技术提升,可能铸钢辊更适合进行焊接修复。
关于双辊速比,现在已经有很多公司加大了速比,虽然产量显著增加,但也带来功率的增加以及胶粉“焦烧”的隐患,速比的加大是一个趋势,需要找到一个平衡点,而且辊筒的冷却设计需要加强,可以考虑在双辊的上方增加喷雾状水装置对于沟辊沟槽的角度设计优化、沟槽深度宽度及形状设计都需要进一步优化;同样,从以前的480辊,到560辊,再到现在有些公司设计的660辊,从800长到1000长到1200长度,加大了直径、长度,增加了转速,加大了速比,这些都是为了提高单机产能需要进行的技术升级改进,但是辊筒的冷却是各生产厂下一步都必须要改进的。
5. 橡胶磨粉机:
关于40目-120目胶粉以及精细胶粉的生产,其实现在的橡胶磨粉机,在常温下是可以生产到80目-120目的,我做过一个测试,从磨粉机进料5-15目(其中5-8目占60%以上),出料后经过气流分选机分离出80目(80目过筛率达到80%以上),然后再把这些80目的胶粉再一次进入到磨粉机里,出料后再一次经过气流分选机分离出120目(120目过筛率达到85%以上)。目前主要是精细胶粉的应用市场没有完全打开,所以即使生产到这种细度也没有太大作用。
现在橡胶磨粉机的现状怎样?如果进料5-15目(其中5-8目占60%以上),出料要求达到国家标准(GB/T19208-2008)80目胶粉的话,一台装机功率30千瓦的橡胶磨粉机产量只有约60公斤/小时,生产过程中还需要添加隔离剂才能达到。由于单机产量很低,经常会看到当客户需要年处理1万吨轮胎并且出料要求60目以上胶粉的话,需要配置十几台橡胶磨粉机。
有人可能会问,为什么不能设计大功率或者大直径的磨盘,以提高单机产能?磨粉机最关键的问题是刀盘的冷却,现在市面上的磨粉机直径大多在280、320等,我以前设计过最大直径550,原以为产量会很高,但是最终测试结果是温度上升太快,产量反而比280的还低。显然,橡胶磨粉机的发展方向必须是往“大直径磨盘、大功率单机”方向发展,至于冷却方式,除了对现在刀盘目前沿用的内循环冷却方式进行更合理的改进外,在进料处增加喷雾状水装置是必然之选。
此外,刀盘的实际工作剪切和磨削长度不要太长,并且磨盘的磨道设计要简单,不要想到让胶粒在磨盘中间走复杂的流道,而要让胶粒进入到剪切和磨削区域后尽快出料。
事实上,在国内粉碎废旧轮胎制成精细胶粉及改性沥青有着巨大潜力可供发掘,其延伸应用和进一步深加工势将形成一个蓬勃发展的朝阳产业,成为未来新的经济增长点,作为生产粉碎设备的企业也必将进入到高速发展通道,也将助力我国交通、化工等相关行业飞速发展。